(接上期)
4.3.3结论
通过退捻加捻法与直接计数法的比对试验,及对各试验参数对捻度值的影响与分析,为使退捻加捻法与直接计数法试验结果相统一,笔者认为:
4.3.3.1允许伸长的确定应该是随机抽取5只管纱,舍弃卷装的始端或尾端各数米长,每只管纱做一次断裂瞬间的伸长值。在确定每次值、平均值时,均以整数计数。在确定允许伸长值时,捻度试验仪的长度尺分度值1mm,其分辨力可达到0.5mm,则在数据修约时可修约到5的倍数。
4.3.3.2由对比试验可以证明,转速对捻度的影响是不显著的,还不如误差的影响大。因而为体现退捻加捻法简洁快速的特点,将转速提高至1500r/min是完全可行的。
4.3.3.3不分纱线的线密度,以线密度的相同可相近的倍数确定预加张力,一律以0.50±0.10cN/tex进行设置,形成了很多情况下退捻加捻法与直接计数法测试结果的不一致。合理的办法可根据纱线不同的设计捻度,将纱线线密度大致分成几个范围,根据不同的线密度范围,分别以不同的线密度倍数设置预加张力。
4.4结合两种方法,保证捻度测试的准确性
由以上可以看出,从检验结果的准确性或测试的可操作性而言,捻度试验单一采用退捻加捻法难以得到保证。结合两种捻度测试方法,取长补短,相互结合,是捻度测试的正确程序。建议:
1)不要把捻度试验的退捻加捻法列为一个完全独立的标准,单一地采用这种试验方法都不能保证捻度检验结果的准确性与可操作性。新产品上机进行捻度试验时,应该采用直接计数法法做捻度试验作为第一程序,再进行退捻加捻法试验,通过几次两者捻度值的差异对比,根据预加张力与捻度值的相互关系,确定退捻加捻法准确的预加张力。
2)因直接计数法操作的难度,捻度试验通过两试验方法对比确定预加张力后,日常检验采用退捻加捻法,但应定期进行与直接计数法的对比,遇有重大工艺参数变动,或原料发生重大变化,都应用直接计数法确定退捻加捻法采用的预加张力。
3)现行的试验方法的隔距长度是原试验方法隔距长度的两倍,要先做允许伸长的五次试验,且退捻、加捻速度变慢,新捻度试验方法较GB/T2543.2-1989检验时间大幅度增加。为此我们为探讨不同试验次数对捻度值的影响,对于不同的样品进行了不同试验次数的比对试验,检验结果见表3
从以上可以看出,不同的试验次数一组样品的离散性不同,但均值差异很小,因纱线不同片段或有不同的离散性,因而不同试验次数的这种差异可以看作是纱线不同的离散性造成的,而不是因试验次数的不同造成。
原试验方法隔距长度L=250mm,n=40次,新的试验方法L=500mm, n=40次,实际上n=20次即达到了GB/T2543.2-1989的试验长度,现行的纱线标准对捻度的考核,均是列出了一个捻系数的控制范围,没有考核捻系数变异系数,仅考核捻度平均值;就捻度平均值的的准确性而言,达到原标准的相应捻度试验长度,其捻度平均值的准确性是等同的,那么按照现行的捻度试验方法,考核捻度平均值,n=20次即可满足标准要求。
5.气流纺(转杯纺)纱捻度测试标准—前版本为FZ/T10001—1989,现行版本FZ/T10001—2006
5.1转杯纺纱加捻及结构的特殊性 转杯纺纱属于自由端纺纱,棉条由喂给罗拉和喂给板喂入后,被分梳辊开松成单纤维状态。在气流(分为自排风式与抽气式气流)的作用下,纤维沿着一个渐缩形的通道进入转杯,纤维则沿转杯壁斜面滑移至离心力最大的凝聚槽内,形成周向排列的须条。引纱(即形成自由端的部分)从引纱管吸入即甩至凝聚槽,与已凝聚的须条相接触,随着纺杯的回转而加捻。引纱与须条搭接在一起,随着引纱的输出,须条离开凝聚槽,引纱的捻度被传递给须条,形成转杯纱。转杯纱加捻过程的特点决定了转杯纱径向捻度的分层分布, 转杯纱径向的捻度分布规律取决于须条的凝聚方式和捻度在须条轴向上的分布情况。
转杯纺在转杯中形成环形须条,它的有捻部分仅在凝聚槽剥离点之后的一段距离内,而单纤维以相同的几率沿凝聚槽的整个圆周分布凝聚,形成从剥离点起逐渐变细的须条。在须条截面中捻度的径向分布规律就呈现出中心部分捻度较少,然后向外逐渐增加,自截面径向某个范围开始(这个范围取决于须条有捻部分的长度)捻度又逐渐减少,直至外层,从而形成转杯纱截面内各层的捻度不一。
这种独特的成纱原理,形成转杯纺纱外层具有很多的包缠纤维(包缠纤维的多少与纺杯大小有直接关系,见图1),虽然这些包缠纤维与环锭纺毛羽有所不同,但同样影响织物外观质量与织物风格,转杯纺纱的表面的包缠纤维在纱样退绕过程中容易被破坏, 且各层捻度不一致.转杯纺纱与环锭纺纱结构不同,这对转杯纺纱的捻度检测方法提出了特殊的要求。
5.3.4结论
FZ/T10001-1992中的b法步骤复杂,检验时间长;试验结果与其a法相比,因试验参数的不同设置,特别是对捻度值影响较大的预加张力的不同设置,形成两种试验方法对同一纱线捻度值试验结果不等。但两者也具有一定的相关性,两种方法虽有差异,但其差异趋势是一致的,因b法的预加张力是a法预加张力的二倍,即b法的试验结果普遍大于a法的试验结果。另一方面,由于转杯纺纱加捻的特殊方式及转杯纺设备的非理想状态,形成捻度损失,并因各种纤维模量的不同及设计捻度的大小不同,形成转杯纺纱实际捻度与设计捻度的不同差异,故使转杯纺实际捻度不可能等于设计捻度,更不可能大于设计捻度。b法的捻度值大于设计捻度,这在理论上无法解释,也与转杯纺纱实际捻度明显不符。
5.4转杯纺纱应用FZ/T10001—2006与GB/T2543.2的比对试验
新的转杯纺纱捻度测试方法“气流纱捻度的测定 退捻加捻法”FZ/T10001-2006,相比FZ/T10001—1992,删除了三次退捻加捻法,规定用一次退捻加捻法作为转杯纺纱捻度的测试方法,这与等效采用ISO标准的“纺织品 纱线捻度的测定 第二部分:退捻加捻法”GB/T2543.2-2001的测试原理相同,只是部分参数设置略有差异,则其测试结果应该紧密相关,我们通过一组对比试验,探讨转杯纺纱捻度测试应用GB/T2543.2-2001捻度的可行性。
5.4.1试验准备
5.4.1.1样品选取:本试验选取五个品种:COE18.2texK COE27.8texT COE36.4texT
COE58.3tesW COE58.3tesT
5.4.1.2执行标准: GB/T2543.2-2001 FZ/T10001-2006
5.4.1.3温湿度控制:意大利HIROSS恒温恒湿机组
温度:20℃±1.0℃ 湿度:65±2%RH
5.4.1.5取样数量与试验次数:为减少不同筒纱间的离散性对试验结果的影响,每个品种取一个筒纱进行试验;为减少一个样品不同片段的离散性对试验结果的影响,本试验进行重复试验10次,各样品检验结果以10次平均值进行比较分析。因有些品种是无角度筒子,不易分清方向,不同方向退绕会引起加捻或退捻,增加试验中的不确定度,本试验不管筒子有无角度,测试时一律以面对筒子顺时针方向退绕作为正向退绕。
5.4.1.6试验计划:本试验先用GB/T2543.2-2001进行每品种测试,再用FZ/T10001-2006进行每品种测试,因FZ/T10001-2006中设置转速为1500r±200/min,与GB/T2543.2-2001的1000±200r/min有一定差异,为精确比对两捻度测试方法的相关性,再用FZ/T10001-2006采用GB/T2543.2-2001设置的
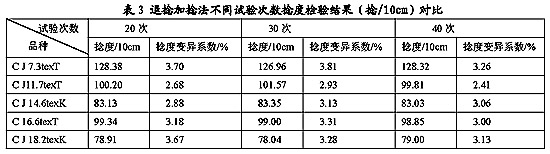
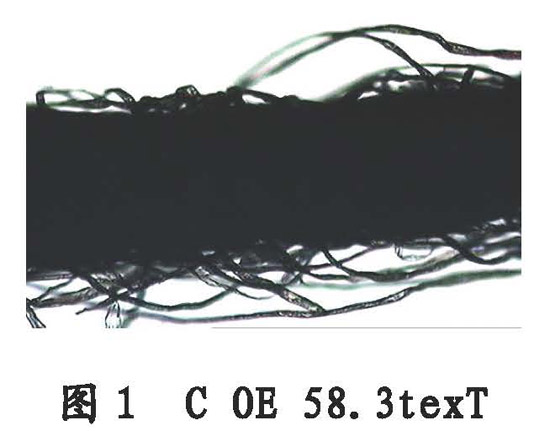
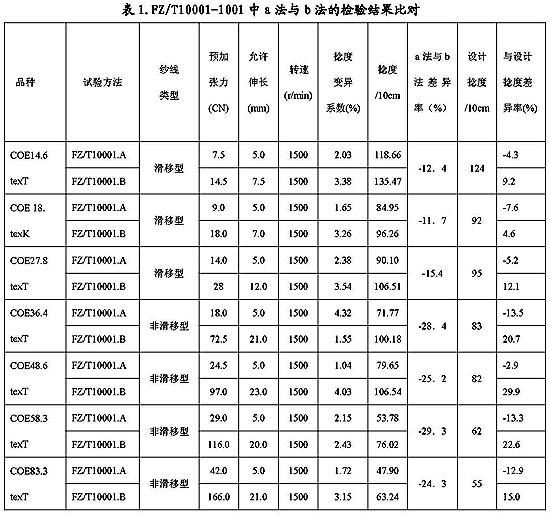
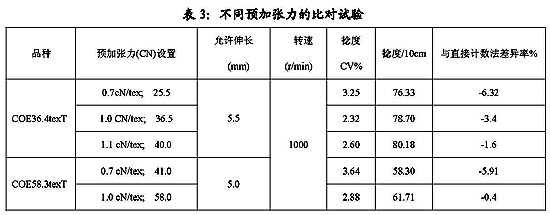
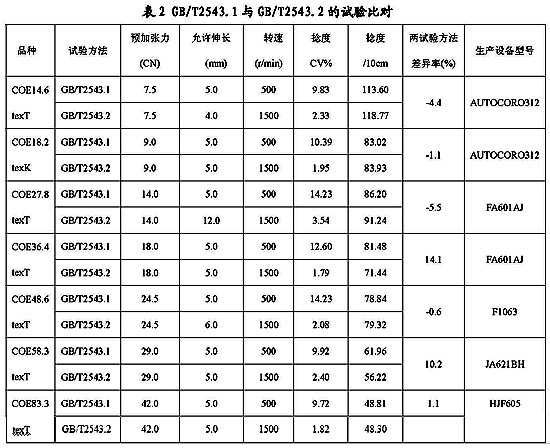
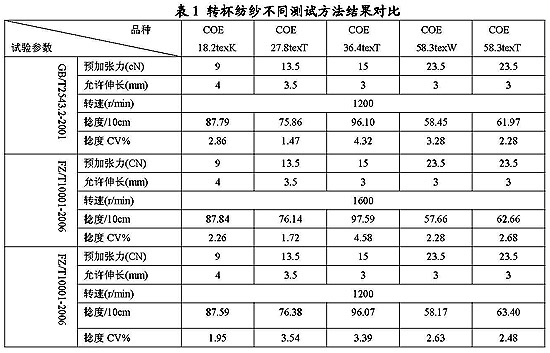
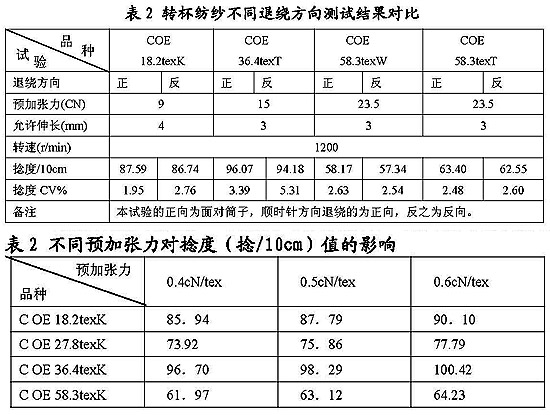